Innovationen in der Doppelspur-Fertigung erhöhen Durchsatz und Flexibilität
Zu den derzeit wichtigsten Märkten für Elektronikhersteller gehören IoTAnwendungen (Internet of Things) und die Elektrifizierung des Automobils, die sich
durch eine stark steigende Nachfrage nach verschiedensten Elektronik-Geräten
auszeichnen.
Laut ResearchGate sind bereits mehr als 50 Milliarden IoT-Geräte wie intelligente
Smarthome-Monitore, Wearables und Industriesensoren mit dem Internet verbunden
– und jedes Jahr kommen über 10 Milliarden weitere hinzu.
Im Automobilbereich schreitet die Elektrifizierung immer schneller voran, um die
Wirtschaftlichkeit zu verbessern, Emissionen zu senken, die Sicherheit zu erhöhen
und das Fahrerlebnis weiter zu steigern. Immer ausgefeiltere Infotainment- und
Fahrerüberwachungssysteme, moderne Fahrerassistenzsysteme (ADAS),
elektronisch gesteuerte Beleuchtung und elektrischer Antrieb bedeuten, dass neue
Fahrzeugmodelle buchstäblich Hunderte von Baugruppen enthalten, die mit
Prozessoren, Kommunikations-ICs, Leistungshalbleitern, Hochleistungs-LED-Arrays
und mehr bestückt sind.
Die Anzahl und Vielfalt dieser technologisch fortschrittlichen Geräte, die in unseren
digitalen Lebensstil integriert sind, durchbrechen die klassische Aufteilung der
Elektronikfertigungen in High-Mix/Low-Volume- und Low-Mix/High-VolumeProduktionen. OEMs und EMS-Unternehmen müssen eine Vielzahl
unterschiedlicher Produkttypen (High-Mix) in großen Mengen (High-Volume)
herstellen und dabei stets eine hohe Produktivität aufrechterhalten.
Doppelspur-SMT
Doppelspur-Maschinen für die Oberflächenmontage scheinen hier eine Lösung zu
bieten, da sie die gleichzeitige Montage von Baugruppen in beiden Spuren
ermöglichen. Dies hilft den Herstellern in mehrfacher Hinsicht, auf schnell
wachsende Märkte zu reagieren.
Erstens ermöglicht die Doppelspur-Technologie eine schnelle Skalierung der
Produktionskapazität und eine höhere Effizienz. Durch den simultanen Betrieb von
zwei Spuren können mehr Leiterplatten in der gleichen Zeit verarbeitet werden, so
dass höhere Stückzahlen produziert werden können.
Zweitens ermöglicht die Doppelspurigkeit den Herstellern eine effiziente
Verarbeitung einer großen Anzahl unterschiedlicher Produkttypen. Jede Spur kann
für ein bestimmtes Produkt oder eine bestimmte Produktvariante konfiguriert
werden. So können verschiedene Typen gleichzeitig produziert werden. Diese
Flexibilität ist von entscheidender Bedeutung in Märkten, in denen eine breite
Palette an Produkttypen mit unterschiedlichen Spezifikationen und Merkmalen
gefordert ist.
Drittens trägt die doppelspurige Montage dazu bei, die Flächenausnutzung in der
Fabrik zu optimieren, indem der Produktionsdurchsatz erhöht wird, ohne den
Platzbedarf der Maschinen wesentlich zu vergrößern.
Die Hersteller müssen einen großen Produktmix in erheblichen Stückzahlen
herstellen und dabei wettbewerbsfähige Stückkosten und eine pünktliche Lieferung
gewährleisten. Für diese Herausforderung bietet die Doppelspur-Montage eine
kostengünstige und platzsparende Lösung. Durch die evolutionären Veränderungen
der neuesten Doppelspur-Systeme ist das Equipment in der Lage, die
Leistungsvorteile zu erbringen, die es schon immer versprochen hat.
Durchsatz trifft auf Flexibilität
Bei der neuesten Maschinen-Generation, wie den Doppelspur-Maschinen der YRSerie von Yamaha, haben beide Spuren die gleiche Priorität, da sie über den
gleichen Parameter-Einstellbereich verfügen und die gleichen automatischen
Funktionen unterstützen.
Der doppelspurige Schablonendrucker YRP10DL und der doppelspurige Bestücker
YRM20DL erlauben im Doppelspur-Modus eine maximale Baugruppenbreite von
330 mm (Bild 1). Daher können beide Systeme direkt miteinander verbunden
werden. In der Vergangenheit hat ein Doppelspur-Drucker eventuell zwei getrennte
Bestücker über kundenspezifische Transportsysteme bedient, die jedoch die
Komplexität und die Kosten der Linie erhöht haben. Alternativ dazu konnte ein
einzelner Drucker die Leiterplatten über ein aufteilendes Transportsystem in eine
doppelspurige Bestückungsmaschine übergeben.

Die maximale Transportbreite von 330 mm ist größer als bei typischen
Vorgängermodellen und ermöglicht so größere Nutzenformate, die zusätzliche
Leiterplatten (PCBs) aufnehmen können (Bild 2a). Ebenso können Trägersysteme
für flexible gedruckte Schaltungen (FPCs) 50 % mehr Einheiten enthalten ( Bild 2b),
indem sie die Vorteile der erhöhten Transportbreite nutzen.

Bestück-Modi
Der Bestücker YRM20DL bietet mehrere Montage-Betriebsarten, um die
Produktivität zu erhöhen. Dazu gehören parallele und alternierende Bestück-Modi
mit zwei separaten Montagebereichen sowie die Flexibilität der Over-DriveTechnologie. Diese Features erweitern den kollisionsfreien Arbeitsbereich des
Kopfes, um die Wartezeit für die Montage im alternierenden Modus zu verkürzen
und so die Produktivität zu steigern. Im Parallel-Modus verkürzt das in 4 Abschnitte
aufgeteilte Transportsystem die Länge des jeweiligen Transportweges. Die
parallelen und alternierenden Modi ermöglichen optional verlängerte
Transportsegmente für bis zu 380 mm.
Im Parallelmodus können die beiden Spuren komplett unabhängig voneinander
betrieben werden – mit je eigener Rüstung. Ein Nonstop-Wechsel der Feederbänke
ist möglich, ohne dafür die Linie anzuhalten. So können Betreiber der Linie ein
Produkt der Spur 1 zuordnen und gleichzeitig das gleiche oder ein anderes Produkt
der Spur 2 zuordnen, wobei Rüstwechsel an beiden Spuren unabhängig von der
jeweils anderen jederzeit möglich sind. Der Parallel-Modus ist vor allem bei der
Herstellung von Baugruppen mit einer geringen Anzahl verschiedener Bauteiltypen
sinnvoll.
Im alternierenden Modus können beide Köpfe Bauteile auf beiden Spuren platzieren
und die Feeder werden für beide Spuren gemeinsam genutzt. Beide Spuren können
das gleiche Produkt oder verschiedene Produkte produzieren. So können auch
Baugruppen bestückt werden, die eine große Vielfalt an Bauteiltypen enthalten,
auch wenn die Zykluszeit kurz sein soll. Die gemeinsame Verwendung von
Bauteilen und die Angleichung der Produktivität sind möglich.
Darüber hinaus kann das YRM20DL im Hybrid-Modus betrieben werden, um den
Fall zu bedienen, dass auf jeder Spur ein anderes Produkt hergestellt wird und eine
der beiden Baugruppen mit mehr Bauteilen bestückt ist als die andere. Im HybridModus kann der geringer ausgelastete Kopf Bauteile auf der anderen Spur
platzieren, um die Zykluszeit zu verkürzen. Dies ermöglicht zusätzliche Flexibilität,
falls die Produktionskapazität Priorität hat und die aufgerüsteten Positionen der
Feeder für den Parallelbetrieb nicht geeignet sind. Die gemeinsame Verwendung
von Bauteilen und die Angleichung der Produktivität sind auch im Hybrid-Modus
möglich.
Die Produktions-Modi der einzelnen Bestücker innerhalb einer Linie können
unabhängig voneinander geändert werden, um die Produktivität zu maximieren und
eine effiziente Nutzung der Feeder-Positionen zu gewährleisten. Dies ermöglicht
eine Mixed-Modus-Produktion, bei der, wie in Bild 3 gezeigt, der Parallel-Modus für
die Chipmontage und der alternierende Modus für die Montage von Odd-ShapedBauteilen genutzt werden, die viele Feederplätze benötigen. Bild 3 zeigt auch einen
alternierenden Modus, der nur auf einer Seite angewandt wird, um Odd-ShapedBauteile zu montieren.
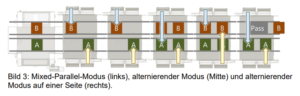
Der Bestücker YRM20DL verfügt auch über hochmoderne Funktionen des
bestehenden Einspur-Modells, mit verbesserter Baugruppen-Transferkapazität und
stopperloser Baugruppen-Positionierung. Die Forderung nach einer stopperlosen
Positionierung stammt ursprünglich aus der Automobilbranche, um die Integrität von
Baugruppen besser zu schützen. Der Bestücker verknüpft außerdem die Aktivierung
der Unterstützungsstifte mit dem Klemmen der Baugruppe und koordiniert beide
Vorgänge, um den Zeitaufwand für den Baugruppen-Transfer zu minimieren.
Darüber hinaus ermöglichen der Non-Stop-Programm- und der Non-StopFeederwagen-Wechsel eine schnelle Umrüstung zwischen aufeinanderfolgenden
Produkten.
Der Non-Stop-Programm-Wechsel maximiert die Effizienz in jedem Fall, egal, ob die
Baugruppenbreite und die Positionen der Unterstützungsstifte gleich sind oder
verschieden. Wenn die Spurbreite des eingehenden Auftrags und die Position der
Unterstützungsstifte übereinstimmen, kann die Maschine einfach die aktuelle
Baugruppe fertigstellen und das Programm für den nächsten Auftrag umstellen.
Wenn jedoch die Spurbreite oder die Position der Unterstützungsstifte
unterschiedlich sind, lässt die Maschine die ankommende Baugruppe vor der
Maschine warten. Die neue Spurbreite wird eingestellt, nachdem die letzte
Baugruppe des aktuellen Auftrags die Maschine verlassen hat.
Der Non-Stop-Feederwagen-Wechsel ermöglicht ein sicheres Entfernen und
Ersetzen der Feederwagen, ohne die Maschine anzuhalten. Eine Spur kann die
Produktion fortsetzen, während auf der anderen Spur die automatische Einrichtung
der Feederwagen läuft. Dadurch können die beiden Spuren unabhängig
voneinander betrieben werden, wobei jede Spur einen anderen Produktmix
produzieren kann.
Durchgängig nahtlose Doppelspur-Linie
Der Doppelspur-Drucker YRP10 DL bietet ebenfalls flexible Einstellungen für die
Spurbreiten und automatische Funktionen, die auf jeder Spur aktiv sind. Wenn diese
Maschinen zusammen eingesetzt werden, kann die gesamte SMT-Montagelinie mit
zwei voneinander völlig unabhängigen Spuren betrieben werden. Sie gewähren
maximale Flexibilität und höchsten Durchsatz, unabhängig davon, ob ein geringer
oder hoher Mix an Produkttypen zu produzieren ist.
Der Drucker arbeitet als ‚zwei parallele Inline-Schablonendrucker‘, die jeweils völlig
unabhängig voneinander operieren. Beide unterstützen einen vollautomatischen
Programmwechsel, um Stillstandszeiten kurz zu halten und die Produktivität zu
maximieren.
Die Inspektionsmaschine YRi-V DL bietet ebenfalls zwei Spuren und verfügt über
ein neu entwickeltes Transportsystem mit verfahrbaren Spuren, was die Ankopplung
an andere vor- oder nachgelagerte Inline-Maschinen erheblich vereinfacht.
Die Maschine kann einen weiten Bereich an Baugruppenbreiten verarbeiten, bis zu 320
mm x 2 im Doppelspur-Modus. Darüber hinaus sind kundenspezifische
Baugruppenformate bis zu 1200 mm x 610 mm möglich. Wenn beide Spuren kleine
Baugruppen inspizieren, können die Spuren nahe beieinander angeordnet werden,
um die Verfahrzeit des Prüfkopfes beim Spurwechsel zu minimieren.
Die YRi-V verfügt außerdem über neue Algorithmen, die die Inspektion von
Lötstellen gemäß den IPC-Richtlinien noch weiter verbessern. Zudem gibt es
aktualisierte Kameraeinstellungen, um die Anforderungen der neuesten
Halbleitergehäuse, wie z. B. das Wafer-Level-Chip-Scale-Package (WL-CSP), zu
bewältigen. Deren Gehäuseoberflächen neigen zu Reflexionen, die die
Möglichkeiten herkömmlicher Inspektionsgeräte übersteigen ( Bild 4).
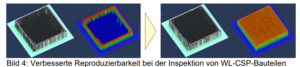
Weitere Verbesserungen sind ein 8-Winkel-3D-Kamera-Array, das die Bilderfassung
beschleunigt und eine 4-Winkel-Kamera mit 20 Megapixeln zur Erfassung
hochauflösender Bilder von Merkmalen wie Lötstellen. Es ist bekannt, dass es für
herkömmliche Inspektions-Maschinen nicht leicht ist, diese genau zu erfassen und
zu bewerten.
Wenn diese Maschinen zusammen in der gleichen Linie verwendet werden,
bedeuten der doppelspurige Drucker, der doppelspurige Bestücker und die
doppelspurige Inspektions-Maschine eine durchgängig nahtlose
Doppelspurfertigung auf dieser Linie. Um dies zu erreichen, waren in der
Vergangenheit verschiedene Kombinationen einspuriger Maschinen erforderlich, die
mit speziellen Transportsystemen verbunden waren, was zu einem komplexen
Linienlayout führte, das oft teuer und zeitaufwändig in der Planung und Installation
ist.
Fazit
Die stark steigende Nachfrage nach einer großen Anzahl verschiedener
Produkttypen in großen Stückzahlen, die von den heute am schnellsten wachsenden
Märkten ausgeht, ist ein starkes Plädoyer für die doppelspurige
Oberflächenmontage. Die neueste Maschinengeneration maximiert das
Leistungspotenzial der Doppelspur-Technik, um den Produktionsdurchsatz, die
Flexibilität und die Produktivität zu steigern.
Über Yamaha Robotics SMT Section
Die Yamaha Surface Mount Technology (SMT) Section, eine Unterabteilung der
Yamaha Motor Robotics Business Unit der Yamaha Motor Corporation, produziert
eine umfassende Palette von Systemen für die Hochgeschwindigkeits-InlineElektronikmontage. Diese 1 STOP SMART SOLUTION umfasst Lotpastendrucker,
Bestückungsautomaten, 3D-Lotpasteninspektionsmaschinen, 3DBaugruppeninspektionsmaschinen, Flip-Chip-Hybrid-Bestücker, Dispenser,
intelligente Bauteillagerung und Management-Software.
Diese Systeme, die den Yamaha-Ansatz in die Elektronikfertigung bringen, legen
den Schwerpunkt auf eine intuitive Bedienerführung, eine effiziente Koordination
zwischen allen Inline-Prozessen und eine Modularität, die es Anwendern
ermöglicht, die neusten Fertigungsanforderungen zu erfüllen. Die Kompetenzen
der Gruppe bei der Steuerung von Servomotoren und der Kamera-basierten
Bildverarbeitungssysteme gewährleisten extreme Genauigkeit bei hoher
Geschwindigkeit.
Die aktuelle Produktlinie umfasst die neueste YR-Maschinengeneration mit
hochentwickelten Automatisierungsfunktionen für die Programmierung,
Einrichtung und Umrüstung sowie die neue YSUP-Managementsoftware mit
hochmodernen Grafiken und integrierter Datenanalyse.
Durch die Bündelung der Kompetenzen in den Bereichen Design und Technik,
Herstellung, Vertrieb und Service gewährleistet die Yamaha SMT Section
betriebliche Effizienz und einen einfachen Support-Zugang für Kunden und
Partner. Mit regionalen Niederlassungen in Japan, China, Südostasien, Europa
und Nordamerika bietet das Unternehmen eine wahrhaft globale Präsenz.
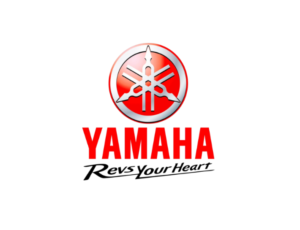