Neue Analysetools für SMT- Baugruppen minimieren Stillstandszeiten und
erhöhen die Effizienz der Produktionslinie, indem sie Fehler-Ursachen
identifizieren und Korrekturmaßnahmen vorschlagen
Obwohl die Oberflächenmontage mit großer Präzision und Zuverlässigkeit
verbunden ist, kann es bei kontinuierlichem Betrieb mit hoher Geschwindigkeit auch
zu Fehlern kommen. Tritt ein Fehler auf, muss das für die Produktion verantwortliche
Team schnellstmöglich den ordnungsgemäßen Betriebszustand wiederherstellen.
Immer wenn die Linie angehalten wird, entstehen Kosten, die die Rentabilität
beeinträchtigen. Diese Kosten umfassen nicht nur die direkten Kosten für
Produktionsausfälle, sondern auch die Arbeitskosten während des Stillstands der
Linie, die Kosten für Überstunden und Eilaufträge, um nach der Wiederherstellung
der Linie aufzuholen, sowie die Kosten für Nacharbeit oder Baugruppen, die
aufgrund des Problems, das den Stillstand verursacht hat, verschrottet werden
mussten. Selbst die Wartezeiten im Lagerbestand verursachen Kosten, und die
Störung des normalen Betriebsablaufs kann zu Ineffizienzen führen. Darüber hinaus
kann es Auswirkungen auf zugesagte Liefertermine geben, die ggf. zu
Konventionalstrafen führen können.
Andererseits kann es wichtig sein, die Linie schnell zu stoppen, wenn ein Problem
erkannt wird, um zu verhindern, dass die Produktion defekter Einheiten fortgesetzt
wird. Der Bediener und/oder die Produktionsleitung muss im Fehlerfall so schnell
wie möglich Bescheid wissen. Linienstillstände sind unerwünscht und der Betreiber
muss sicherstellen, dass diese so selten wie möglich vorkommen, um die beste
Produktivität sicherzustellen und entsprechende Kosten zu minimieren. Ist ein
Stillstand unvermeidlich, muss die Produktion so schnell wie möglich
wiederhergestellt werden.
Tools zur Findung von Fehlerursachen
Moderne Montagesysteme sind mit Sensoren ausgestattet, die Probleme wie
verstopfte Nozzeln oder Pickup-Fehlausrichtungen erkennen können. Die
automatische, optische Inspektion kann an mehreren Punkten in der Linie
durchgeführt werden, einschließlich nach dem Schablonendruck, der Bauteilplatzierung und dem Reflowlöten, wobei die Inspektions-Ergebnisse zur
Unterstützung der Fehlerbehebung in Echtzeit verwendet werden.
Baugruppen-Hersteller vertrauen hier auf Software-Tools, um Produktionsanlagen
zu verwalten, Abweichungen und Fehler zu erkennen und Informationen für den
verantwortlichen Mitarbeiter bereitzustellen. Dazu gehören DashboardAnwendungen, die eine sofortige Beurteilung der Anlagen und des
Produktionsstatus ermöglichen. Es gibt auch Mehrwert-Tools wie Yamahas QAOptionen und die eng verwandte Mobile Judgement-App. Mobile Judgement kann
Details beliebiger erkannter Mängel, einschließlich Inspektionsbilder, direkt an das
Smartphone des Verantwortlichen senden, der dann die Schwere des Problems
bewertet. Nach persönlicher Einschätzung kann dann der Verantwortliche bei Bedarf
einen sofortigen Stopp der Linie anweisen, bis das Problem gelöst wurde.
Die Mensch/Maschine-Schnittstelle
Die Mensch/Maschine-Schnittstelle ist derjenige Teil der Software, durch den
Maschinen und Menschen interagieren, um Probleme zu lösen, die im normalen
Produktionsverlauf auftreten können. Das verantwortliche Team muss seine
Fähigkeiten einsetzen, um die geforderte Menge jeder Charge zu liefern und
sicherzustellen, dass die Produktion termingerecht läuft.
Dieses Konzept kann von der Qualität der Werkzeuge abhängen, die zur
Visualisierung der an den verschiedenen Stellen der Linie erfassten Daten
bereitgestellt werden. Die Ermittlung der Fehlerursachen und die rasche Behebung
hängen auch von den Fähigkeiten und Kenntnissen der Vorgesetzten ab, die in der
Fabrik tätig sind. Wenn der leitende Vorgesetzte aus irgendeinem Grund nicht im
Dienst ist – vielleicht arbeitet er in einer anderen Schicht, ist im Urlaub oder vielleicht
krankgeschrieben – könnte die Produktivität beeinträchtigt werden.
Die jüngsten Fortschritte in den Informationswissenschaften können dazu beitragen,
Abhängigkeiten von individuellen Einschätzungen zu beseitigen, indem die
Ursachen von Fehlern oder anderen Produktionsproblemen automatisch ermittelt
werden. Wenn die Bediener direkt zu den Problemursachen geführt werden, ist eine
konsistentere Produktionsleistung möglich. Beispielsweise enthält Yamahas
neuestes Analyse-Dashboard YSUP innovative Werkzeuge, die mit Hilfe
statistischer Methoden die wahrscheinlichsten Ursachen für festgestellte Fehler
ermitteln. Das Tool empfiehlt auch geeignete Abhilfemaßnahmen. Die Analysetools
arbeiten mit grafischen Werkzeugen zusammen, mit denen die Leistung der Anlagen
in der Produktionslinie visualisiert wird (Bild 1).
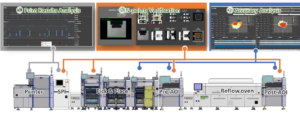
Bild 1: Visualisierungstools der Dashboards erleichtern die Bewertung der
Prozessleistung
Das Analyse-Dashboard YSUP präsentiert Informationen in leicht lesbarer Form, die
auf einen Blick interpretiert werden können. So kann jede Arbeitsschicht einen
konsistent-hohen Durchsatz bei gleichbleibender Linienausbeute und drastisch
reduzierter Stillstandszeit erzielen.
Auf der Grundlage einer relationalen Datenbank mit integrierten Abfrage-Funktionen,
die Daten « in situ » analysieren, identifiziert die Software mithilfe statistischer
Verfahren wahrscheinliche Ursachen für aufgezeichnete Fehler nahezu in Echtzeit.
Die automatischen Analyse-Funktionen der neuen Dashboard-Anwendung
ermöglichen es autorisierten Benutzern, jederzeit benötigte Informationen zu
extrahieren, Fehler zu analysieren und Vorschläge zu Korrekturmaßnahmen zu
sehen.
Zu den verfügbaren Werkzeugen gehört die automatische Pickup-Fehleranalyse, bei
der Analysemethoden wie Flow-Judgement, Fehlercode-Diagnose, Health-CheckDaten-Diagnose und Bilderkennungs-Diagnose zum Einsatz kommen. Der Benutzer
kann den Zeitpunkt und die Umstände von Pickup-Fehlern, den genauen Ort und
vorgeschlagene Korrekturmaßnahmen einsehen (Bild 2). Yamaha hat die
Genauigkeit der automatischen Pickup-Fehleranalyse mit diesem Tool in
gemeinsamen Experimenten mit einem Großkunden, einem Tier-1-Hersteller der
Automobilindustrie, verifiziert. Darüber hinaus gibt es auch integrierte Funktionen,
die bei der Erkennung von Ursachen helfen, einschließlich der Verwaltung
automatischer Beurteilungsergebnisse und der Nachverfolgung von
Gegenmaßnahmen.
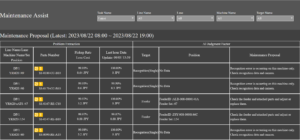
Bild 2: Analyse von Pickup-Fehlern, einschließlich Lokalisierung und
Korrekturmaßnahmen.
Die Leistungsreserven der zugrundeliegenden Plattform bieten die Möglichkeit,
weitere Analysetools, wie z. B. Platzierungsanalyse und Druckanalyse,
hinzuzufügen. Darüber hinaus ist die Plattform offen für den Einsatz künstlicher
Intelligenz (KI) in künftigen Ausgaben, die zusätzliche Analysemöglichkeiten bietet
und Problemlösungen direkt an den Produktionslinien weiter beschleunigt.
Fazit
Fortschritte in der Automatisierung haben es Elektronikherstellern ermöglicht,
zahlreiche Tätigkeiten an den Produktionslinien von menschlichen Einschränkungen
zu befreien. Ein manuelles Eingreifen ist jedoch nach wie vor erforderlich, wenn es
darum geht, auf außergewöhnliche Umstände zu reagieren und den
ordnungsgemäßen Betrieb wiederherzustellen. Die neuesten datengesteuerten
Dashboard-Tools bieten zusätzliche Unterstützung bei der Ermittlung und Behebung
von Fehlerursachen. Sie helfen, Begrenzungen durch lückenhafte Kenntnisse der
Bediener zu überwinden und verkürzen die Zeit bis zur Wiederherstellung des
Betriebs, was letztlich eine weitere Verbesserung der Produktivität ermöglicht.
Über Yamaha Robotics SMT Section
Die Yamaha Surface Mount Technology (SMT) Section, eine Unterabteilung der
Yamaha Motor Robotics Business Unit der Yamaha Motor Corporation, produziert
eine umfassende Palette von Systemen für die Hochgeschwindigkeits-InlineElektronikmontage. Diese 1 STOP SMART SOLUTION umfasst Lotpastendrucker, Bestückungsautomaten, 3D-Lotpasteninspektionsmaschinen, 3DBaugruppeninspektionsmaschinen, Flip-Chip-Hybrid-Bestücker, Dispenser,
intelligente Bauteillagerung und Management-Software.
Diese Systeme, die den Yamaha-Ansatz in die Elektronikfertigung bringen, legen
den Schwerpunkt auf eine intuitive Bedienerführung, eine effiziente Koordination
zwischen allen Inline-Prozessen und eine Modularität, die es Anwendern
ermöglicht, die neusten Fertigungsanforderungen zu erfüllen. Die Kompetenzen
der Gruppe bei der Steuerung von Servomotoren und der Kamera-basierten
Bildverarbeitungssysteme gewährleisten extreme Genauigkeit bei hoher
Geschwindigkeit.
Die aktuelle Produktlinie umfasst die neueste YR-Maschinengeneration mit
hochentwickelten Automatisierungsfunktionen für die Programmierung,
Einrichtung und Umrüstung sowie die neue YSUP-Managementsoftware mit
hochmodernen Grafiken und integrierter Datenanalyse.
Durch die Bündelung der Kompetenzen in den Bereichen Design und Technik,
Herstellung, Vertrieb und Service gewährleistet die Yamaha SMT Section
betriebliche Effizienz und einen einfachen Support-Zugang für Kunden und
Partner. Mit regionalen Niederlassungen in Japan, China, Südostasien, Europa
und Nordamerika bietet das Unternehmen eine wahrhaft globale Präsenz.
https://yamaha-motor-robotics.de
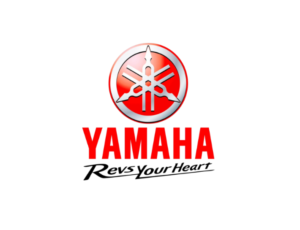